图书介绍
精益产品开发体系 丰田整合人员、流程与技术的13项精益原则PDF|Epub|txt|kindle电子书版本下载
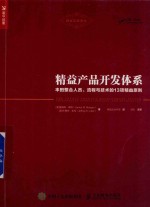
- (美)詹姆斯·摩根(JamesM.Morgan),(美)杰弗瑞·莱克(JeffreyK.Liker)著;精益企业中国译 著
- 出版社: 北京:人民邮电出版社
- ISBN:9787115445001
- 出版时间:2017
- 标注页数:341页
- 文件大小:38MB
- 文件页数:360页
- 主题词:丰田汽车公司-工业企业管理-经验
PDF下载
下载说明
精益产品开发体系 丰田整合人员、流程与技术的13项精益原则PDF格式电子书版下载
下载的文件为RAR压缩包。需要使用解压软件进行解压得到PDF格式图书。建议使用BT下载工具Free Download Manager进行下载,简称FDM(免费,没有广告,支持多平台)。本站资源全部打包为BT种子。所以需要使用专业的BT下载软件进行下载。如BitComet qBittorrent uTorrent等BT下载工具。迅雷目前由于本站不是热门资源。不推荐使用!后期资源热门了。安装了迅雷也可以迅雷进行下载!
(文件页数 要大于 标注页数,上中下等多册电子书除外)
注意:本站所有压缩包均有解压码: 点击下载压缩包解压工具
图书目录
第一部分 引言1
第1章 新产品开发的革命3
1.1 下一场战役:产品开发体系5
1.2 卓越的产品开发:下一个核心竞争力8
1.3 精益产品开发体系:将不同领域、部门及供应商串联起来9
1.4 为什么独独挑中丰田10
1.5 向丰田学习12
第2章 精益产品开发体系模型14
2.1 社会技术系统14
2.2 流程子系统:精益产品开发体系原则1至原则416
2.3 人员子系统:精益产品开发体系原则5至原则1020
2.4 工具及技术子系统:精益产品开发体系原则11至原则1322
第二部分 流程子系统25
第3章 明确由客户定义的价值,将增值与浪费区分开来27
3.1 北美汽车公司的客户价值定义流程28
3.2 丰田的客户价值定义流程29
3.3 案例:雷克萨斯车身团队将误差容限降低了一半32
3.4 为什么这是第一原则36
第4章 在产品开发流程前期充分研究可选方案38
4.1 设计工厂的前期重点投入:通过管理产品平台将各个开发项目关联起来40
4.2 在现有产品平台上推出的衍生产品41
4.3 先进技术计划43
4.4 单个项目内部的前期重点投入:造型和工程可行性45
4.5 多方案并行工程46
4.6 丰田车身和结构工程——研讨50
4.7 实例:将执行层面的活动标准化能使问题解决得更加快捷52
4.8 通用架构和重复使用原则的应用53
4.9 评估和确定整车层面的目标54
4.10 丰田生产工程:同步工程师的职责55
4.11 同步工程师必须实现投资和可变成本目标56
4.12 借助数字化工具58
4.13 案例分析:研讨中的早期问题解决59
4.14 K4整合63
4.15 正确的人,正确的工作,正确的时间63
第5章 建立一个均衡的产品开发流程65
5.1 “流”的力量65
5.2 把产品开发看作一个流程66
5.3 产品开发流程中的七种浪费70
5.4 真正的3M72
5.5 流动的促进因素和阻碍因素:排队论的启示74
5.6 均衡流始于“模糊”的初始阶段:研讨和流79
5.7 流程逻辑的角色80
5.8 工作量均衡、周期计划与资源配置81
5.9 产品开发的执行阶段83
5.10 跨功能同步和功能内同步83
5.11 创建柔性产能85
5.12 制订详细计划以避免不均衡87
5.13 功能组织层面的详细计划88
5.14 错开发布,实现跨功能部门的流动88
5.15 在非传统制造中创建过程流89
5.16 在产品开发体系中拉动知识93
5.17 把一切汇入“流”中94
第6章 利用严格的标准化减少变异,创建柔性和可预测的产出97
6.1 标准化的三种类型98
6.2 第一类:设计标准化和工程检查清单99
6.3 第二类:流程标准化102
6.4 第三类:标准化的技能集/能力110
6.5 结论111
第三部分 人员子系统113
第7章 建立自始至终领导项目开发的总工程师制度115
7.1 总工程师制度背后的文化象征116
7.2 两位总工程师的传奇:雷克萨斯和普锐斯119
7.3 总工程师的领导力模式129
7.4 北美汽车公司的产品开发经理:从总工程师到官僚132
7.5 克莱斯勒的小组召集133
7.6 丰田的总工程师体制:避免导致官僚主义的妥协134
第8章 通过组织来平衡功能专长与跨功能整合137
8.1 这是最佳的组织结构吗137
8.2 用矩阵组织结构管理产品开发流程的优点和缺点140
8.3 丰田原创的矩阵组织:将两种结构相融合的长期传统141
8.4 克莱斯勒的平台团队结构:与车辆开发中心的对比146
8.5 并行工程:作战室150
8.6 同步工程:模块开发团队以及总生产工程师152
8.7 组织——不断进化的流程157
第9章 为工程师构造尖塔形的知识结构159
9.1 选聘、培养并留住人才的理念160
9.2 北美汽车公司的招聘及录用流程161
9.3 丰田的员工发展164
9.4 “现地现物”工程169
9.5 精益产品开发体系必须培养人171
第10章 将供应商完全整合到产品开发体系中174
10.1 零件不仅仅是零件,供应商也不仅仅是供应商175
10.2 合作伙伴:各有所得184
10.3 外包政策的关键189
10.4 对待供应商要通情达理193
第11章 企业内部学习和持续改善197
11.1 定义知识和组织的学习197
11.2 丰田产品开发的学习网络199
11.3 从经验中学习201
11.4 视问题为机会204
11.5 无知:最终的代价207
第12章 建立追求卓越、锐意进取的企业文化210
12.1 如何架起精益企业的文化桥梁210
12.2 工具并非解决方案214
12.3 为客户、社会和社区作出贡献214
12.4 卓越的工程技术深植于文化中215
12.5 学习的基因222
12.6 向上、向下和横向的管理:“报-联-相”式管理224
12.7 正确的流程产生正确的结果226
12.8 企业文化支持作业流程226
12.9 领导者建立企业的文化229
第四部分 工具与技术子系统231
第13章 调整技术以适应人员和流程233
13.1 选择工具和技术的五个重要原则233
13.2 精益产品开发中的技术235
13.3 制造工程和工装制造的工具241
13.4 善用技术以强化开发流程248
第14章 运用直观、可视化的沟通方式来理顺组织250
14.1 总工程师的概念书:形成具有一致性的文件251
14.2 跨功能部门的作战室252
14.3 整合的工具254
14.4 丰田解决问题的A3工具259
14.5 丰田的沟通与整合266
第15章 运用强大的工具做好标准化和组织学习268
15.1 你的组织如何学习268
15.2 北美汽车公司的知识数据库:车身开发价值流269
15.3 丰田的技术数据库270
15.4 沟通与评价的方法272
15.5 北美汽车公司的竞争对手标杆分析报告275
15.6 丰田的竞争产品拆解和分析表276
15.7 丰田的标准化工具:工程检查表、质量矩阵、制造图和标准化工艺流程图278
15.8 标准化与学习工具的角色280
第16章 一个连贯的系统:化零为整283
16.1 子系统集成:人员、流程、工具和技术284
16.2 识别价值:提供客户定义的价值285
16.3 推动价值流:消除浪费和变异286
16.4 建立拉动方式和“流”289
16.5 尽善尽美:在开发中融入学习和持续改善291
16.6 跨功能整合292
第17章 消除产品开发价值流中的浪费294
17.1 产品开发价值流图分析295
17.2 PDVSM工作小组会310
17.3 学习将产品开发看作一个流程312
第18章 开始文化转型:精益产品开发的核心314
18.1 培养一位内部变革推动者316
18.2 获得所需的知识316
18.3 确定可管理的工作流,将产品开发视为一个流程317
18.4 一体化的机制(作战室/设计审查)318
18.5 功能机构的参与319
18.6 从客户出发319
18.7 掌握精益产品开发流程的现状320
18.8 推动真正的文化转变323
18.9 人员:精益产品开发体系的核心326
18.10 精益转型路线图327
18.11 领导力、学习型组织和持续改善331
附录 价值流图分析法在产品开发流程中的应用:PeopleFlo制造公司案例333
译后记339