图书介绍
实用机械加工工艺手册PDF|Epub|txt|kindle电子书版本下载
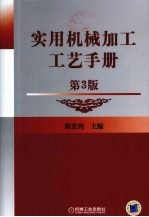
- 陈宏钧主编 著
- 出版社: 北京:机械工业出版社
- ISBN:9787111257714
- 出版时间:2009
- 标注页数:1785页
- 文件大小:508MB
- 文件页数:1816页
- 主题词:机械加工-工艺-技术手册
PDF下载
下载说明
实用机械加工工艺手册PDF格式电子书版下载
下载的文件为RAR压缩包。需要使用解压软件进行解压得到PDF格式图书。建议使用BT下载工具Free Download Manager进行下载,简称FDM(免费,没有广告,支持多平台)。本站资源全部打包为BT种子。所以需要使用专业的BT下载软件进行下载。如BitComet qBittorrent uTorrent等BT下载工具。迅雷目前由于本站不是热门资源。不推荐使用!后期资源热门了。安装了迅雷也可以迅雷进行下载!
(文件页数 要大于 标注页数,上中下等多册电子书除外)
注意:本站所有压缩包均有解压码: 点击下载压缩包解压工具
图书目录
第1章 机械制造常用名词术语1
1 机械制造工艺基本术语1
1.1 一般术语1
1.2 典型表面加工术语1
1.3 冷作、钳工及装配常用术语9
2 热处理名词术语11
3 机械制造工艺管理名词术语17
3.1 工艺管理术语17
3.2 工艺装备管理术语17
3.3 质量管理和质量保证术语18
3.4 定置管理术语22
第2章 机械加工工艺规程的设计及现场工艺管理23
第1节 机械加工工艺规程的编制23
1 机械加工工艺规程的作用23
2 机械加工工艺过程的组成23
3 机械加工工艺规程的制订23
3.1 工艺规程制订原则23
3.2 制订工艺规程所需原始资料23
3.3 工艺规程制订程序24
4 工艺过程设计中应考虑的主要问题24
4.1 定位基准选择24
4.2 零件表面加工方法的选择25
4.2.1 加工方法选择的原则25
4.2.2 各类表面的加工方案及适用范围25
4.3 加工顺序的安排27
4.3.1 加工阶段的划分27
4.3.2 工序的合理组合27
4.3.3 加工顺序的安排27
5 工序设计28
5.1 工序基准的选择28
5.2 工序尺寸的确定28
5.2.1 确定工序尺寸的方法28
5.2.2 工艺尺寸链的计算参数与计算公式28
5.2.3 工艺尺寸链的基本类型与工序尺寸的计算30
5.3 加工余量的确定36
5.4 机床的选择37
5.5 工艺装备的选择38
5.6 切削用量的选择38
5.7 时间定额的确定38
6 工艺文件格式及填写规则38
6.1 机械加工工艺过程卡片格式及填写规则38
6.2 机械加工工序卡片格式及填写规则40
6.3 标准零件(或典型零件)工艺过程卡片格式及填写规则40
第2节 零件图样的工艺性审查43
1 产品结构工艺性审查43
1.1 产品结构工艺性审查内容和程序43
1.2 零件结构工艺性的基本要求44
2 零件结构的切削加工工艺性45
2.1 工件便于在机床或夹具上装夹的图例45
2.2 减少装夹次数的图例46
2.3 减少刀具调整与走刀次数的图例46
2.4 采用标准刀具减少刀具种类的图例46
2.5 减少切削加工难度的图例46
2.6 减少加工量的图例52
2.7 加工时便于进刀、退刀和测量的图例52
2.8 保证零件在加工时刚度的图例52
2.9 有利于改善刀具切削条件与提高刀具寿命的图例52
3 一般装配对零部件结构工艺性的 要求57
3.1 组成单独部件或装配单元57
3.2 应具有合理的装配基面58
3.3 考虑装配的方便性59
3.4 考虑拆卸的方便性59
3.5 考虑装配的零部件之间结构的合理性60
3.6 避免装配时的切削加工61
3.7 选择合理的调整补偿环62
3.8 减少修整外形的工作量62
4 零件结构的热处理工艺性63
4.1 防止热处理零件开裂的结构要求63
4.2 防止热处理零件变形及硬度不均的结构要求65
4.3 热处理齿轮零件的结构要求68
第3节 典型零件机械加工工艺过程举例69
1 轴类零件69
1.1 调整偏心轴69
1.2 单拐曲轴70
1.3 连杆螺钉73
2 套类零件75
2.1 缸套75
2.2 活塞76
2.3 偏心套78
3 齿轮、花键、丝杆类零件80
3.1 齿轮80
3.2 锥齿轮81
3.3 齿轮轴82
3.4 矩形齿花键轴84
3.5 矩形齿花键套85
3.6 丝杆86
4 连杆类零件88
4.1 两孔连杆88
4.2 三孔连杆91
5 箱体类零件93
5.1 减速器93
5.2 曲轴箱97
6 其他类零件101
6.1 轴承座101
6.2 带轮102
6.3 轴瓦103
第4节 生产现场工艺管理及工艺纪律105
1 生产现场工艺管理105
1.1 生产现场工艺管理的主要任务和内容105
1.2 生产现场定置管理方法及考核106
2 工艺纪律管理106
2.1 基本要求106
2.2 工艺纪律的主要内容106
2.3 工艺纪律的考核107
第3章 机械加工质量108
第1节 机械加工精度108
1 影响加工精度的因素及改善措施108
1.1 影响尺寸精度的因素及改善措施108
1.2 影响形状精度的因素及改善措施108
1.3 影响位置精度的因素及改善措施108
2 各种加工方法的加工误差111
3 机械加工的经济精度112
3.1 加工路线与所能达到的公差等级和表面粗糙度112
3.2 各种加工方法能达到的尺寸经济精度112
3.3 各种加工方法能达到的形状经济精度118
3.4 各种加工方法能达到的位置经济精度118
第2节 机械加工表面质量121
1 表面粗糙度121
1.1 各种加工方法能达到的表面粗糙度121
1.2 影响加工表面粗糙度的因素及改善措施122
1.3 表面粗糙度与加工精度和配合之间的关系122
1.4 各种连接表面的粗糙度125
2 加工硬化与残余应力125
2.1 加工表面层的冷作硬化125
2.2 残余应力127
3 机械加工中的振动127
3.1 强迫振动的特点、产生原因与消减措施127
3.2 自激振动(颤振)的特点、产生原因与消减措施127
第4章 机械制图129
第1节 基本规定129
1 图纸幅面和格式129
1.1 图纸幅面尺寸129
1.2 图框格式及尺寸129
2 标题栏和明细栏130
2.1 标题栏方位130
2.2 标题栏131
2.3 明细栏131
3 比例132
3.1 术语132
3.2 比例系列132
3.3 标注方法132
4 字体132
4.1 基本要求132
4.2 字体示例133
5 图线135
6 剖面符号139
第2节 图样画法139
1 视图139
1.1 基本视图名称及其投影方向的规定139
1.2 视图的类型140
2 剖视142
2.1 剖视图142
2.2 剖切面142
2.3 剖切符号144
2.4 剖视图的配置144
2.5 剖切位置与剖视图的标注144
3 断面图145
4 局部放大图146
5 简化画法147
5.1 基本要求147
5.2 特定简化画法148
5.3 对称画法150
5.4 剖切平面前、后结构及剖面符号简化画法150
5.5 轮廓画法151
5.6 相同、成组结构或要素的画法152
5.7 特定结构或要素的画法153
5.8 特定件画法154
第3节 尺寸注法156
1 基本规则156
2 标注尺寸三要素156
2.1 尺寸数字156
2.2 尺寸线157
2.3 尺寸界线159
3 标注尺寸的符号160
4 简化注法162
4.1 简化注法基本规定162
4.2 简化注法图例162
第4节 常用零件画法166
1 螺纹及螺纹紧固件166
1.1 螺纹的规定画法166
1.2 螺纹的标注167
1.3 装配图中螺纹紧固件的画法169
1.4 常用紧固件的简化画法170
2 齿轮、齿条、蜗杆、蜗轮及链轮的画法171
2.1 齿轮、齿条、蜗轮及链轮的画法171
2.2 齿轮、蜗杆、蜗轮啮合画法172
3 矩形花键的画法及其尺寸标注173
4 弹簧的画法174
4.1 螺旋弹簧的画法174
4.2 碟形弹簧的画法174
4.3 平面涡卷弹簧的画法175
4.4 板弹簧的画法175
4.5 装配图中弹簧的画法175
5 中心孔表示法175
5.1 中心孔符号175
5.2 中心孔在图样上的标注175
6 滚动轴承表示法175
6.1 基本规定175
6.2 简化画法182
6.3 规定画法187
6.4 应用示例187
7 动密封圈表示法188
7.1 基本规定188
7.2 简化画法188
7.3 规定画法194
7.4 应用举例194
第5章 机械零件195
第1节 螺纹195
1 普通螺纹(M)195
1.1 普通螺纹牙型195
1.2 普通螺纹直径与螺距系列195
1.3 普通螺纹的基本尺寸198
1.4 普通螺纹的公差201
1.5 标记方法及示例211
2 梯形螺纹(30°)(Tr)212
2.1 梯形螺纹牙型212
2.2 梯形螺纹直径与螺距系列213
2.3 梯形螺纹基本尺寸213
2.4 梯形螺纹公差215
2.5 梯形螺纹旋合长度220
2.6 梯形螺纹代号与标记221
3 锯齿形螺纹(3°、30°)(B)221
3.1 锯齿形(3°、30°)螺纹牙型221
3.2 锯齿形螺纹的直径与螺距系列222
3.3 锯齿形螺纹基本尺寸222
3.4 锯齿形螺纹公差224
3.5 锯齿形螺纹标记方法及示例228
4 55°管螺纹228
4.1 55°密封管螺纹228
4.2 55°非密封管螺纹231
5 60°密封管螺纹232
5.1 螺纹术语及代号232
5.2 螺纹牙型及牙型尺寸232
5.3 圆锥管螺纹的基本尺寸及其公差233
5.4 圆柱内螺纹的基本尺寸及公差234
5.5 有效螺纹的长度235
5.6 倒角对基准平面理论位置的影响235
5.7 螺纹特征代号及标记示例235
6 米制管螺纹(60°)236
6.1 一般密封米制管螺纹(ZM、M)236
6.2 非密封米制管螺纹(M)237
7 英制惠氏螺纹237
7.1 牙型237
7.2 英制惠氏螺纹的标准系列238
7.3 基本尺寸238
7.4 公差239
7.5 标记示例241
第2节 齿轮241
1 渐开线圆柱齿轮241
1.1 基本齿廓和模数241
1.2 圆柱齿轮的几何尺寸计算242
1.3 齿轮精度244
1.4 齿轮检验项目263
1.5 齿厚263
1.6 侧隙263
1.7 中心距和轴线平行度264
1.8 齿轮的接触斑点264
1.9 齿面表面粗糙度的推荐值265
1.10 齿轮坯的精度265
1.11 GB/T 10095—1988版渐开线圆柱齿轮精度267
2 齿条276
2.1 齿条的几何尺寸计算276
2.2 齿条精度276
3 锥齿轮282
3.1 锥齿轮基本齿廓尺寸参数282
3.2 模数282
3.3 直齿锥齿轮几何尺寸计算282
3.4 锥齿轮精度285
3.5 锥齿轮及锥齿轮副公差表290
3.6 锥齿轮齿坯要求302
4 圆柱蜗杆和蜗轮303
4.1 圆柱蜗杆的类型及基本齿廓303
4.2 圆柱蜗杆的主要参数304
4.3 圆柱蜗杆传动几何尺寸计算309
4.4 圆柱蜗杆、蜗轮精度311
4.5 蜗杆、蜗轮及其传动的公差表317
4.6 齿坯要求324
第3节 键、花键和销325
1 键325
1.1 平键325
1.2 半圆键330
1.3 楔键333
1.4 切向键337
2 花键339
2.1 花键连接的类型、特点和使用339
2.2 矩形花键340
2.2.1 矩形花键尺寸系列340
2.2.2 矩形花键的公差与配合342
2.2.3 标记示例343
2.3 圆柱直齿渐开线花键343
2.3.1 渐开线花键的模数系列343
2.3.2 渐开线花键标准压力角344
2.3.3 渐开线花键术语、代号及定义344
2.3.4 渐开线花键的基本尺寸计算公式345
2.3.5 外花键大径基本尺寸346
2.3.6 渐开线花键公差与配合349
2.3.7 图样标记示例349
2.3.8 公差数值表349
3 销360
3.1 销的类型及应用范围360
3.2 常用销的规格尺寸362
第4节 链和链轮366
1 滚子链传动366
1.1 滚子链的结构形式和规格尺寸366
1.2 滚子链用附件367
1.3 滚子链链轮367
1.3.1 滚子链链轮齿槽形状367
1.3.2 三圆弧一直线齿槽形状和尺寸计算370
1.3.3 滚子链链轮轴向齿廓及尺寸371
1.3.4 滚子链链轮的基本参数和主要尺寸371
1.3.5 链轮公差371
1.3.6 滚子链链轮常用材料及热处理373
2 齿形链传动373
2.1 齿形链的基本参数和尺寸373
2.2 齿形链链轮373
2.2.1 链轮齿形与基本参数373
2.2.2 齿形链链轮轴向齿廓尺寸373
2.2.3 齿形链链轮检验项目及公差373
2.2.4 齿形链链轮轮坯公差373
第5节 滚动轴承377
1 滚动轴承的分类377
2 滚动轴承代号的构成378
2.1 基本代号378
2.2 前置、后置代号383
2.3 轴承代号示例386
3 常用滚动轴承型号及外形尺寸举例386
3.1 深沟球轴承386
3.2 调心球轴承389
3.3 双列圆柱滚子轴承390
3.4 圆锥滚子轴承392
3.5 双列圆锥滚子轴承393
3.6 角接触球轴承394
3.7 推力球轴承397
4 滚动轴承的配合398
第6节 圆锥和棱体399
1 锥度、锥角及基公差399
1.1 圆锥的术语及定义399
1.2 锥度与锥角系列400
1.3 圆锥公差402
2 棱体404
2.1 棱体的术语及定义404
2.2 棱体的角度与斜度系列406
第7节 常用零件结构要素406
1 中心孔406
1.1 60°中心孔406
1.2 75°、90°中心孔408
2 各类槽409
2.1 退刀槽409
2.2 砂轮越程槽411
2.3 润滑槽413
2.4 T形槽414
2.5 燕尾槽416
3 零件倒圆与倒角416
4 球面半径417
5 螺纹零件417
5.1 紧固件外螺纹零件末端417
5.2 普通外螺纹收尾、肩距、退刀槽和倒角尺寸418
5.3 普通内螺纹收尾、肩距、退刀槽和倒角尺寸419
5.4 普通螺纹的内、外螺纹余留长度、钻孔余留深度和螺栓突出螺母的末端长度420
5.5 紧固件用通孔和沉孔422
5.6 梯形螺纹的收尾、退刀槽和倒角尺寸424
5.7 米制锥螺纹的结构要素425
5.8 圆柱管螺纹的收尾、退刀槽和倒角尺寸426
第6章 常用材料及热处理428
第1节 钢428
1 金属材料性能的名词术语428
2 钢的分类429
3 钢牌号表示方法430
3.1 牌号表示方法的基本原则430
3.2 钢铁材料的名称及其符号431
3.3 钢牌号表示方法的举例432
4 常用钢的品种、性能和用途435
4.1 结构钢435
4.1.1 碳素结构钢435
4.1.2 优质碳素结构钢436
4.1.3 低合金高强度钢439
4.1.4 合金结构钢440
4.1.5 易切削结构钢451
4.1.6 非调质机械结构钢452
4.1.7 弹簧钢452
4.2 工具钢454
4.2.1 碳素工具钢454
4.2.2 合金工具钢455
4.2.3 高速工具钢458
4.3 轴承钢460
4.4 特种钢461
4.4.1 不锈钢461
4.4.2 耐热钢467
5 型钢471
5.1 热轧圆钢和方钢尺寸规格471
5.2 热轧六角钢和八角钢尺寸规格471
5.3 冷拉圆钢、方钢、六角钢尺寸规格473
5.4 热轧扁钢的尺寸规格474
5.5 优质结构钢冷拉扁钢的尺寸规格476
5.6 热轧等边角钢的尺寸规格476
5.7 热轧不等边角钢的尺寸规格478
5.8 热轧工字钢的尺寸规格479
5.9 热轧槽钢的尺寸规格480
6 钢板和钢带481
6.1 热轧钢板和钢带481
6.2 冷轧钢板和钢带483
6.3 不锈钢热轧钢板484
6.4 不锈钢冷轧钢板485
6.5 锅炉用钢板的牌号、板厚及力学和工艺性能487
6.6 压力容器用钢板的牌号、板厚及力学和工艺性能487
7 钢管488
7.1 无缝钢管488
7.2 结构用无缝钢管495
7.3 结构用不锈钢无缝钢管497
7.4 不锈钢冷拔(轧)小直径无缝钢管的尺寸规格500
7.5 直缝电焊钢管501
8 钢丝504
8.1 重要用途低碳钢丝504
8.2 优质碳素结构钢丝505
8.3 合金结构钢丝506
8.4 碳素工具钢丝507
8.5 合金工具钢丝507
8.6 高速工具钢丝508
8.7 碳素弹簧钢丝508
8.8 重要用途碳素弹簧钢丝509
8.9 合金弹簧钢丝510
8.10 油淬火—回火弹簧钢丝510
8.11 熔化焊用钢丝512
8.12 气体保护焊用钢丝512
8.13 焊接用不锈钢丝513
9 常用钢的火花鉴别法513
10 钢材的标记515
10.1 钢材的标记代号515
10.2 钢材的涂色标记515
第2节 铸钢517
1 一般工程用铸造碳钢517
2 焊接结构用碳素钢铸件518
3 合金铸钢件518
4 高锰钢铸件的牌号、力学性能和适用范围520
5 工程结构用中、高强度不锈钢铸件520
6 一般用途耐热钢和合金铸件521
第3节 铸铁522
1 铸铁的分类522
2 铸铁牌号表示方法522
2.1 铸铁名称、代号及牌号表示方法522
2.2 铸铁牌号表示方法举例523
3 常用铸铁的性能和用途523
3.1 灰铸铁523
3.2 球墨铸铁523
3.3 可锻铸铁525
3.4 蠕墨铸铁526
3.5 耐热铸铁526
3.6 高硅耐蚀铸铁528
3.7 耐磨铸铁528
3.8 抗磨白口铸铁529
第4节 有色金属及其合金530
1 有色金属及其合金产品代号表示方法530
2 铜及铜合金532
2.1 加工铜的牌号、代号及主要特性和应用举例532
2.2 加工黄铜的牌号、代号及主要特性和应用举例532
2.3 加工青铜的牌号、代号及主要特性和应用举例532
2.4 加工白铜的牌号、代号及主要特性和应用举例538
2.5 铜及铜合金力学性能539
2.6 铜及铜合金工艺性能541
3 铸造铜合金542
4 铝及铝合金547
4.1 变形铝及铝合金的新旧牌号对照547
4.2 常用铝及铝合金加工产品的牌号及主要特性和应用举例548
4.3 铝及铝合金热处理工艺参数552
5 铸造铝合金553
5.1 铸造铝合金的牌号、代号和力学性能553
5.2 铸造铝合金的主要特性和应用举例556
5.3 铸造铝合金热处理工艺规范558
6 铸造轴承合金558
第5节 粉末冶金材料559
1 粉末冶金材料的分类及应用举例559
2 粉末冶金铁基结构材料560
3 粉末冶金摩擦材料562
4 粉末冶金减摩材料牌号及力学性能564
5 烧结不锈钢过滤元件565
第6节 非金属材料567
1 工程塑料及其制品567
1.1 常用工程塑料的性能特点及应用567
1.2 工程塑料棒材567
1.3 工程塑料管材569
2 橡胶、石棉及其制品571
2.1 常用橡胶的特性及用途571
2.2 橡胶、石棉制品573
第7节 热处理575
1 热处理工艺分类及代号575
2 热处理工艺576
2.1 钢件的整体热处理576
2.1.1 退火576
2.1.2 正火577
2.1.3 淬火577
2.1.4 回火578
2.1.5 冷处理579
2.2 钢的表面热处理579
2.3 钢的化学热处理579
3 常用金属材料热处理工艺参数580
3.1 优质碳素结构钢常规热处理工艺参数580
3.2 合金结构钢常规热处理工艺参数582
3.3 弹簧钢常规热处理工艺参数587
3.4 碳素工具钢常规热处理工艺参数588
3.5 合金工具钢常规热处理工艺参数590
3.6 高速工具钢常规热处理工艺参数595
3.7 轴承钢常规热处理工艺参数597
第7章 金属切削机床及辅具599
第1节 金属切削机床型号编制方法599
1 通用机床型号表示方法599
1.1 型号表示方法599
1.2 机床的分类及类代号599
1.3 机床的特性代号599
1.4 机床的组、系代号及主参数600
1.5 通用机床的设计顺序号600
1.6 主轴数和第二主参数的表示方法600
1.7 机床的重大改进顺序号600
1.8 其他特性代号及其表示方法600
1.9 企业代号及其表示方法600
1.10 金属切削机床统一名称和类、组、系划分600
2 专用机床的型号600
3 机床自动线的型号600
第2节 通用机床技术参数与辅具614
1 车床614
1.1 常用车床的型号与技术参数614
1.1.1 卧式车床的型号与技术参数614
1.1.2 马鞍车床的型号与技术参数614
1.1.3 立式车床的型号与技术参数614
1.1.4 转塔车床、回轮车床的型号与技术参数614
1.1.5 仿形车床的型号与技术参数614
1.1.6 曲轴车床的型号与技术参数614
1.1.7 数控卧式车床的型号与技术参数614
1.2 普通车床辅具624
1.2.1 刀杆624
1.2.2 刀夹627
1.2.3 加工螺纹用辅具628
2 铣床629
2.1 常用铣床的型号与技术参数629
2.1.1 卧式升降台铣床的型号与技术参数629
2.1.2 万能升降台铣床的型号与技术参数629
2.1.3 立式升降台铣床、数控立式升降台铣床的型号与技术参数629
2.1.4 工具铣床、数控工具铣床的型号与技术参数629
2.1.5 龙门铣床的型号与技术参数629
2.2 铣床辅具636
2.2.1 中间套636
2.2.2 铣刀杆639
2.2.3 铣夹头650
3 钻床652
3.1 常用钻床的型号与技术参数652
3.1.1 台式钻床的型号与技术参数652
3.1.2 立式钻床的型号与技术参数652
3.1.3 摇臂钻床的型号与技术参数652
3.1.4 深孔钻床的型号与技术参数652
3.2 钻床辅具656
3.2.1 过渡套、接长套、夹紧套656
3.2.2 接杆661
3.2.3 刀杆664
3.2.4 夹头669
3.2.5 扁尾锥柄用楔672
4 镗床672
4.1 常用镗床的型号与技术参数672
4.1.1 卧式铣镗床的型号与技术参数672
4.1.2 数控卧式镗床的型号与技术参数672
4.1.3 落地镗床、数控落地铣镗床的型号与技术参数672
4.1.4 坐标镗床的型号与技术参数672
4.1.5 精镗床的型号与技术参数672
4.2 镗床辅具677
4.2.1 镗刀杆677
4.2.2 镗杆689
4.2.3 镗刀架690
4.2.4 接杆692
4.2.5 镗套与衬套694
4.2.6 其他698
5 磨床699
5.1 常用磨床的型号与技术参数699
5.1.1 万能外圆磨床的型号与技术参数699
5.1.2 无心外圆磨床的型号与技术参数699
5.1.3 内圆磨床的型号与技术参数699
5.1.4 卧轴矩台平面磨床的型号与技术参数699
5.1.5 立轴矩台平面磨床的型号与技术参数699
5.1.6 卧轴圆台平面磨床的型号与技术参数699
5.1.7 立轴圆台平面磨床的型号与技术参数699
5.1.8 万能工具磨床的型号与技术参数699
5.1.9 曲轴磨床的型号与技术参数699
5.1.10 花键轴磨床的型号与技术参数699
5.2 磨床辅具724
5.2.1 顶尖724
5.2.2 接杆及螺钉724
6 拉床727
6.1 常用拉床的型号与技术参数727
6.1.1 立式拉床的型号与技术参数727
6.1.2 卧式拉床的型号与技术参数727
6.2 拉床辅具728
6.2.1 接头728
6.2.2 夹头、扳手729
6.2.3 导套、垫片及支座732
7 齿轮加工机床737
7.1 常用齿轮加工机床的型号与技术参数737
7.1.1 滚齿机的型号与技术参数737
7.1.2 插齿机的型号与技术参数743
7.1.3 剃齿机的型号与技术参数744
7.1.4 花键轴铣床的型号与技术参数744
7.2 齿轮加工机床辅具746
7.2.1 滚齿刀杆746
7.2.2 刀垫747
7.2.3 接套747
8 螺纹加工机床748
8.1 专用螺纹车床的型号与技术参数748
8.2 螺纹铣床的型号与技术参数748
8.3 螺纹磨床的型号与技术参数748
8.4 攻丝机的型号与技术参数748
8.5 滚丝机的型号与技术参数752
8.6 搓丝机的型号与技术参数752
9 刨床与插床752
9.1 常用刨床、插床的型号与技术参数752
9.1.1 牛头刨床的型号与技术参数752
9.1.2 单臂刨床的型号与技术参数752
9.1.3 龙门刨床、数控龙门刨床的型号与技术参数752
9.1.4 插床的型号与技术参数752
9.2 刨床辅具752
9.2.1 槽刨刀刀杆752
9.2.2 刨刀刀杆752
10 锯床755
10.1 带锯床的型号与技术参数755
10.2 圆锯床的型号与技术参数755
10.3 弓锯床的型号与技术参数755
第8章 机床夹具758
第1节 通用夹具758
1 顶尖758
1.1 固定顶尖758
1.2 回转顶尖形式及规格758
1.3 内拨顶尖758
1.4 夹持式内拨顶尖762
1.5 外拨顶尖762
1.6 内锥孔顶尖762
1.7 夹持式内锥孔顶尖762
2 夹头764
2.1 鸡心卡头764
2.2 卡环764
2.3 夹板765
2.4 车床用快换卡头765
3 拨盘765
3.1 C型拨盘765
3.2 D型拨盘765
4 卡盘767
4.1 三爪自定心卡盘767
4.2 四爪单动卡盘767
5 过渡盘773
5.1 C型三爪自定心卡盘用过渡盘773
5.2 D型三爪自定心卡盘用过渡盘773
5.3 C型四爪单动卡盘用过渡盘774
5.4 D型四爪单动卡盘用过渡盘774
6 花盘775
7 分度头775
7.1 机械分度头775
7.2 等分分度头775
8 机床用平口台虎钳775
8.1 机床用平口台虎钳规格尺寸775
8.2 角度压紧机用平口台虎钳规格尺寸775
8.3 可倾机用平口台虎钳规格尺寸775
8.4 正弦机用平口台虎钳规格尺寸780
9 常用回转工作台781
10 吸盘781
10.1 矩形电磁吸盘规格尺寸781
10.2 圆形电磁吸盘规格尺寸781
10.3 矩形永磁吸盘规格尺寸781
10.4 圆形永磁吸盘规格尺寸781
10.5 多功能电磁吸盘规格尺寸781
11 铣头、插头、镗头781
11.1 铣头规格尺寸781
11.2 插头规格尺寸781
11.3 镗头规格尺寸781
第2节 专用夹具789
1 机床夹具设计基本要求789
1.1 工件定位原理及其应用789
1.1.1 六点定位原理789
1.1.2 工件的定位要求790
1.1.3 常用定位方法和定位元件所能限制的自由度790
1.1.4 常见加工形式中应限制的自由度794
1.2 对夹紧装置的基本要求796
1.3 夹具的对定797
1.3.1 夹具对切削运动的定位797
1.3.2 夹具对刀具的定位799
1.3.3 夹具分度与转位的对定805
2 机床夹具常用标准零部件806
2.1 定位件806
2.2 导向件816
2.3 支承件824
2.4 夹紧件831
2.5 对刀件844
3 专用夹具典型结构实例846
3.1 车床夹具的典型结构846
3.1.1 车床夹具的特点及设计要求846
3.1.2 车床夹具典型结构的技术参数847
3.1.3 车床夹具类型结构举例849
3.2 钻床夹具857
3.2.1 钻床夹具的特点和主要类型857
3.2.2 钻(镗)床夹具典型结构的技术要求857
3.2.3 钻夹具类型结构举例861
3.3 镗床夹具865
3.3.1 镗床夹具设计要点865
3.3.2 镗床夹具典型结构的技术要求865
3.3.3 镗床夹具类型结构举例865
3.4 铣床夹具866
3.4.1 铣床夹具典型结构的技术要求866
3.4.2 铣床夹具类型结构举例871
3.5 磨床夹具873
第3节 可调夹具875
1 可调整夹具的特点、适用范围与设计要点875
2 可调整夹具结构示例875
第4节 组合夹具878
1 组合夹具的使用范围与经济效果878
2 组合夹具的系列、元件类别及作用878
3 组合夹具典型结构举例880
3.1 钻夹具880
3.2 车夹具882
3.3 铣、刨夹具886
3.4 镗模886
3.5 组合夹具的扩大使用886
第9章 机械加工工序间加工余量890
1 装夹及下料尺寸余量890
1.1 棒材、板材及焊接后的板材结构件各部分加工余量示意890
1.2 夹持长度及夹紧余量890
1.3 下料尺寸余量890
2 轴的加工余量900
2.1 外圆柱表面加工余量及偏差900
2.2 轴端面加工余量及偏差903
2.3 槽的加工余量及公差903
3 内孔加工余量及偏差905
3.1 基孔制7级精度(H7)孔的加工905
3.2 基孔制8级精度(H8)孔的加工906
3.3 用金刚石刀精镗孔加工余量906
3.4 研磨孔加工余量906
3.5 单刃钻后深孔加工余量907
3.6 刮孔加工余量907
3.7 多边形孔拉削余量907
3.8 内花键拉削余量907
4 平面加工余量及偏差907
4.1 平面第一次粗加工余量907
4.2 平面粗刨后精铣加工余量908
4.3 铣平面加工余量908
4.4 磨平面加工余量908
4.5 铣及磨平面时的厚度偏差908
4.6 刮平面加工余量及偏差908
4.7 凹槽加工余量及偏差908
4.8 研磨平面加工余量908
4.9 外表面拉削余量908
5 切除渗碳层的加工余量910
6 齿轮和花键的精加工余量910
6.1 精滚齿和精插齿的齿厚加工余量910
6.2 剃齿的齿厚加工余量910
6.3 磨齿的齿厚加工余量910
6.4 直径大于400mm渗碳齿轮的磨齿齿厚加工余量910
6.5 珩齿加工余量910
6.6 交错轴斜齿轮精加工的齿厚加工余量910
6.7 锥齿轮精加工的齿厚加工余量910
6.8 蜗轮精加工的齿厚加工余量910
6.9 蜗杆精加工的齿厚加工余量910
6.10 精铣花键的加工余量910
6.11 磨花键的加工余量910
7 有色金属及其合金的加工余量912
7.1 有色金属及其合金零件的加工余量912
7.2 有色金属及其合金圆筒形零件的加工余量912
7.3 有色金属及其合金圆盘形零件的加工余量912
7.4 有色金属及其合金壳体类零件的加工余量912
第10章 刀具和磨料磨具916
第1节 刀具材料及刀片916
1 刀具切削部分的材料916
1.1 对刀具切削部分材料性能的要求916
1.2 常用刀具材料916
1.2.1 常用高速钢牌号、力学性能及适用范围916
1.2.2 硬质合金917
1.2.3 陶瓷刀具材料925
1.2.4 超硬刀具材料926
2 刀片927
2.1 硬质合金焊接刀片927
2.1.1 常用焊接车刀刀片927
2.1.2 基本型硬质合金焊接刀片927
2.2 可转位硬质合金刀片940
2.2.1 可转位硬质合金刀片的标记方法940
2.2.2 带圆孔的可转位硬质合金刀片形式及基本尺寸943
2.2.3 无孔可转位硬质合金刀片形式及基本尺寸950
2.2.4 沉孔可转位硬质合金刀片形式及基本尺寸952
2.2.5 硬质合金可转位铣刀片955
2.3 可转位陶瓷刀片的型号与基本参数957
第2节 车刀960
1 刀具切削部分几何角度及其选择960
1.1 刀具切削部分的几何角度960
1.1.1 刀具切削部分的组成960
1.1.2 确定刀具角度的三个辅助平面名称和定义960
1.1.3 刀具的切削角度及其作用961
1.1.4 车刀的工作角度961
1.2 刀具切削部分几何参数的选择963
1.2.1 前角的选择963
1.2.2 车刀前面切削刃和刀尖形状的选择964
1.2.3 后角的选择965
1.2.4 主偏角的选择966
1.2.5 副偏角的选择966
1.2.6 刃倾角的选择967
1.2.7 过渡刃的选择967
2 车刀类型及规格尺寸967
2.1 高速钢车刀条967
2.2 焊接车刀970
2.2.1 硬质合金焊接车刀表示方法970
2.2.2 硬质合金外表面车刀971
2.2.3 硬质合金内表面车刀977
2.3 可转位车刀980
2.3.1 可转位车刀刀片的夹固形式980
2.3.2 可转位车刀型号表示规则981
2.3.3 优先采用的形式和尺寸985
2.3.4 可转位内孔车刀990
2.4 机夹车刀994
2.4.1 机夹切断车刀994
2.4.2 机夹螺纹车刀995
第3节 孔加工刀具997
1 麻花钻997
1.1 标准麻花钻头的切削角度997
1.2 高速钢麻花钻的类型、直径范围及标准代号997
1.3 硬质合金麻花钻类型、直径范围及标准代号1000
1.4 攻螺纹前钻孔用阶梯麻花钻1001
2 可转位钻头类型、直径范围及标准代号1002
3 扩孔钻1003
4 锪钻1004
5 中心钻1005
6 扁钻1007
7 深孔钻1007
7.1 单刃外排屑深孔钻1007
7.2 双刃外排屑深孔钻1007
7.3 单刃内排屑深孔钻1009
7.4 多刃错齿内排屑深孔钻1010
7.5 机夹可转位内排屑深孔钻的形式及加工范围1011
7.6 BTA内排屑深孔钻的形式及加工范围1012
7.7 喷吸钻的结构形式及规格尺寸1012
7.8 DF系统深孔钻的形式及规格尺寸1013
7.9 常用深孔套料钻的类型及特点1014
8 铰刀1015
8.1 铰刀的主要几何参数1015
8.2 常用铰刀形式、标准代号及规格范围1015
第4节 铣刀1019
1 铣刀切削部分的几何形状和角度的选择1019
2 常用铣刀类型、规格范围及标准代号1023
3 可转位铣刀1029
3.1 可转位铣刀片的定位及夹紧方式1029
3.2 可转位铣刀的类型和型号表示方法1030
3.3 可转位铣刀的形式和基本尺寸1032
第5节 螺纹刀具1037
1 丝锥1037
1.1 丝锥的结构和几何参数1037
1.2 常用丝锥的规格范围及标准代号1038
1.3 挤压丝锥1046
1.4 惠氏螺纹丝锥1046
2 板牙1048
2.1 板牙的类型和使用范围1048
2.2 圆板牙的结构和几何参数1048
2.3 管螺纹板牙的结构1049
2.4 常用板牙的规格范围及标准代号1049
3 滚丝轮1051
3.1 普通螺纹滚丝轮的形式及规格尺寸1051
3.2 锥形螺纹滚丝轮基本尺寸1051
4 搓丝板1057
4.1 普通螺纹用搓丝板形式及规格尺寸1057
4.2 60°圆锥管螺纹和55°密封管螺纹搓丝板形式及规格尺寸1059
第6节 齿轮刀具1060
1 盘形齿轮铣刀1060
1.1 盘形齿轮铣刀形式和基本尺寸1060
1.2 盘形锥齿轮铣刀的形式和基本尺寸1062
2 渐开线齿轮滚刀的形式和基本尺寸1062
2.1 小模数齿轮滚刀1062
2.2 整体硬质合金小模数齿轮滚刀1063
2.3 齿轮滚刀1064
2.4 镶片齿轮滚刀1065
2.5 剃前齿轮滚刀1066
2.6 磨前齿轮滚刀1067
2.7 双圆弧齿轮滚刀1068
3 盘形剃齿刀的形式和主要尺寸1069
4 插齿刀1071
4.1 小模数直齿插齿刀的形式和主要尺寸1071
4.2 直齿插齿刀的形式和主要尺寸1073
5 直齿锥齿轮精刨刀1078
第7节 花键和链轮刀具1080
1 花键滚刀的形式和主要尺寸1080
1.1 30°压力角渐开线花键滚刀1080
1.2 45°压力角渐开线花键滚刀1080
1.3 矩形花键滚刀的形式和主要尺寸1081
1.4 渐开线内花键插齿刀1082
2 滚子链和套筒链链轮滚刀基本尺寸1083
第8节 拉刀1084
1 圆推刀的形式和主要尺寸1084
2 键槽拉刀1092
2.1 平刀体键槽拉刀的形式和主要尺寸1092
2.2 加宽平刀体键槽拉刀的形式和主要尺寸1092
2.3 带倒角齿键槽拉刀的形式和主要尺寸1096
2.4 带侧面齿键槽拉力1098
第9节 磨料磨具1101
1 普通磨料磨具1101
1.1 磨料的品种、代号及其应用范围1101
1.2 磨料粒度号及其选择1102
1.3 磨具硬度代号1103
1.4 磨具组织号及其适用范围1103
1.5 结合剂的代号、性能及其适用范围1103
1.6 磨具形状代号和尺寸标记1104
1.7 砂轮的标记方法示例1114
1.8 普通磨具的最高工作速度1115
1.9 普通磨具形状和尺寸1115
2 超硬材料1122
2.1 超硬磨料的品种、代号及应用范围1122
2.2 粒度1122
2.3 超硬磨料结合剂及其代号、性能和应用范围1124
2.4 浓度代号1124
2.5 砂轮、油石及磨头的尺寸代号和术语1124
2.6 砂轮、油石及磨头形状代号1125
2.7 标记示例1129
2.8 超硬材料制品形状代号及主要用途1129
2.9 超硬材料制品1130
2.9.1 金刚石或立方氮化硼磨具形状和尺寸1130
2.9.2 金刚石修整笔1140
3 涂附磨具1141
3.1 页状砂布、砂纸规格尺寸和公差1141
3.2 卷状砂布、砂纸规格尺寸和公差1142
3.3 砂带规格尺寸和公差1142
3.4 砂盘规格尺寸和公差1145
第11章 切削加工1146
第1节 车削加工1146
1 车床加工范围及装夹方法1146
1.1 卧式车床加工1146
1.1.1 卧式车床加工范围1146
1.1.2 卧式车床常用装夹方法1146
1.2 立式车床加工1146
1.2.1 立式车床加工范围1149
1.2.2 立式车床常用装夹方法1150
2 典型零件车削加工实例1151
2.1 车刀的磨损和刃磨1151
2.1.1 刀具磨损的形式1151
2.1.2 车刀磨钝标准及寿命1151
2.1.3 车刀的手工刃磨1151
2.2 标准麻花钻头的磨损和刃磨1153
2.2.1 钻头磨钝标准及寿命1153
2.2.2 标准麻花钻头的刃磨方法及修磨1153
2.3 中心孔的加工与修研1155
2.3.1 中心孔的加工及质量分析1156
2.3.2 中心孔的修研1157
2.4 车削圆锥面1157
2.4.1 锥体各部名称代号及尺寸计算1157
2.4.2 车削圆锥面的方法1158
2.4.3 车削标准锥度和常用锥度时小刀架和靠模板的转动角度1159
2.4.4 车削圆锥面时的尺寸控制方法1159
2.4.5 车削圆锥面时的质量分析1159
2.5 车削偏心工件及曲轴1160
2.5.1 车削偏心工件的装夹方法1160
2.5.2 用专用夹具车削偏心工件1162
2.5.3 测量偏心距的方法1162
2.5.4 车削曲轴的装夹方法1163
2.6 车削成形面1163
2.6.1 成形面车削方法1164
2.6.2 常用成形刀(样板刀)类型及应用1165
2.7 车削球面1166
2.7.1 用蜗杆副传动装置手动车削外球面1166
2.7.2 用蜗杆副传动装置手动车削内球面1166
2.8 车削薄壁工件1167
2.8.1 工件的装夹方法1167
2.8.2 刀具几何角度的选择1168
2.8.3 精车薄壁工件的切削用量1168
2.9 车削表面的滚压加工1168
2.9.1 滚压加工常用工具及其应用1168
2.9.2 滚轮式滚压工具常用的滚轮外圆形状及应用1170
2.9.3 滚轮滚压的加工方法1171
2.9.4 滚压质量分析1171
2.9.5 滚花1172
2.10 冷绕弹簧1173
2.10.1 卧式车床可绕制弹簧的种类1173
2.10.2 绕制圆柱形螺旋压缩弹簧1173
2.10.3 绕制圆柱形螺旋拉伸弹簧1174
2.10.4 绕制圆锥形螺旋压缩弹簧1174
2.10.5 绕制橄榄形弹簧1175
2.11 车削细长轴1175
2.11.1 细长轴的加工特点1175
2.11.2 细长轴的装夹1175
2.11.3 车削细长轴常用的切削用量1178
2.11.4 加工细长轴用车刀举例1178
2.11.5 车削细长轴的质量分析1179
2.12 卧式车床加工常见问题的产生原因及解决方法1180
3 车削用量的选择1180
3.1 硬质合金及高速钢车刀粗车外圆和端面的进给量1180
3.2 硬质合金外圆车刀半精车的进给量1181
3.3 硬质合金及高速钢镗刀粗镗孔进给量1181
3.4 切断及切槽的进给量1183
3.5 成形车削时的进给量1183
3.6 用YT15硬质合金车刀车削碳钢、铬钢、镍铬钢及铸钢时的切削速度1183
3.7 用YG6硬质合金车刀车削灰铸铁时的切削速度1183
3.8 涂层硬质合金车刀的切削用量1185
3.9 陶瓷车刀的切削用量1185
3.10 立方氮化硼车刀的切削用量1187
3.11 金刚石车刀的切削用量1188
第2节 螺纹加工1189
1 车螺纹1189
1.1 螺纹车刀及安装1189
1.1.1 螺纹车刀的类型及应用1189
1.1.2 对三角形螺纹车刀几何形状的要求1190
1.1.3 车螺纹车刀的刀尖宽度尺寸1190
1.1.4 对螺纹车刀安装的要求1190
1.2 卧式车床车螺纹交换齿轮计算1191
1.2.1 车特殊螺距时的计算方法1191
1.2.2 车模数或径节蜗杆时的计算方法1192
1.2.3 车多线螺纹交换齿轮计算及分线方法1192
1.3 螺纹车削方法1194
1.4 常用螺纹车刀的特点与应用1195
1.5 高速钢及硬质合金车刀车削不同材料螺纹的切削用量1199
1.6 高速钢车刀车削螺纹时常用切削液1199
1.7 车削螺纹常见问题、产生原因及解决方法1200
2 旋风铣削螺纹1201
2.1 旋风铣削螺纹的方式及适用范围1201
2.2 旋风铣削螺纹的刀具材料和几何角度1202
2.3 旋风铣削螺纹常用切削用量1202
3 用板牙和丝锥切削螺纹1203
3.1 用板牙套螺纹1203
3.1.1 套螺纹工具1203
3.1.2 工件圆杆直径的确定1203
3.1.3 套螺纹时应注意的事项1204
3.1.4 套螺纹常见问题及防止方法1204
3.2 用丝锥攻螺纹1205
3.2.1 攻螺纹工具1205
3.2.2 攻螺纹切削液选择1206
3.2.3 攻螺纹时应注意的事项1206
3.2.4 攻螺纹前钻孔用麻花钻直径1206
3.2.5 攻螺纹中常见问题1208
4 挤压丝锥挤压螺纹1210
4.1 挤压丝锥的结构、种类及适用范围1210
4.2 挤压螺纹前底孔的确定1210
4.3 挤压螺纹速度的选择1210
5 磨螺纹1210
5.1 螺纹磨削方法1210
5.2 螺纹磨削砂轮选择和修整1211
5.3 螺纹磨削工艺要求1212
第3节 铣削加工1213
1 铣削方式、铣削范围和基本方法1213
1.1 铣削方式1213
1.2 铣削范围和基本方法1214
2 分度头及分度方法1217
2.1 分度头传动系统及分度头定数1217
2.2 分度方法及计算1218
2.2.1 单式分度法计算及分度表1218
2.2.2 角度分度法计算及分度表1219
2.2.3 直线移距分度法1219
3 典型零件的铣削加工1220
3.1 铣削离合器1220
3.1.1 齿式离合器的种类及特点1220
3.1.2 矩形齿离合器的铣削1221
3.1.3 尖齿(正三角形)离合器的铣削1222
3.1.4 梯形收缩齿离合器的铣削1222
3.1.5 锯齿形离合器的铣削1222
3.1.6 梯形等高齿离合器的铣削1224
3.1.7 螺旋齿离合器的铣削1224
3.2 铣削凸轮1225
3.2.1 凸轮传动的三要素1225
3.2.2 等速圆盘凸轮的铣削1226
3.2.3 等速圆柱凸轮的铣削1226
3.3 铣削球面1227
3.4 铣削刀具齿槽1228
3.4.1 对前角γo=0°的铣刀开齿1228
3.4.2 对前角γo>0°的铣刀开齿1229
3.4.3 圆柱螺旋齿铣刀的铣削1230
3.4.4 麻花钻头的铣削1231
3.4.5 端面齿的铣削1231
3.4.6 锥面齿的铣削1232
3.4.7 铰刀的开齿1232
3.5 铣削加工常见问题产生原因及解决方法1233
4 铣削用量的选择1234
4.1 铣刀磨钝标准及寿命1234
4.2 铣削用量1236
4.2.1 高速钢端铣刀、圆柱形铣刀和圆盘铣刀铣削时的进给量1236
4.2.2 高速钢立铣刀、角铣刀、半圆铣刀、切槽铣刀和切断铣刀铣削钢的进给量1236
4.2.3 硬质合金端铣刀、圆柱形铣刀和圆盘铣刀铣削平面和凸台的进给量1237
4.2.4 硬质合金立铣刀铣削平面和凸台的进给量1238
4.2.5 铣削速度1238
4.2.6 涂层硬质合金铣刀的铣削用量1239
第4节 花健、链轮加工1239
1 花键的加工1239
1.1 花键的定心方式及加工精度1239
1.2 在铣床上铣削矩形齿花键轴1240
1.2.1 用单刀铣削矩形齿花键轴1240
1.2.2 用组合铣刀铣削矩形齿花键轴1242
1.2.3 用硬质合金组合刀盘精铣花键轴1242
1.2.4 用成形铣刀铣削花键轴1242
1.3 铣削花键轴时产生误差的原因及解决方法1243
2 铣削链轮1244
2.1 铣削滚子链链轮1244
2.1.1 直线端面齿形滚子链链轮主要尺寸及计算公式1244
2.1.2 直线端面齿形滚子链链轮铣削方法1244
2.1.3 滚子链链轮的测量1246
2.1.4 链轮工作图标注要求1247
2.2 铣削齿形链链轮1247
2.2.1 用单角度铣刀铣削1247
2.2.2 用三面刃铣刀铣削1247
2.2.3 齿形链链轮的测量1247
第5节 齿轮加工1249
1 各种齿轮加工方法1249
2 成形法铣削齿轮1253
2.1 成形铣刀铣直齿圆柱齿轮1253
2.2 成形铣刀铣削直齿条、斜齿条1254
2.3 成形铣刀铣斜齿圆柱齿轮1256
2.4 成形铣刀铣直齿锥齿轮1257
3 飞刀展成铣蜗轮1258
4 滚齿1260
4.1 滚齿机传动系统1262
4.2 常用滚齿机连接尺寸1262
4.2.1 滚齿机主要相关尺寸1262
4.2.2 工作台尺寸1262
4.2.3 刀架及尾架尺寸1263
4.3 常用滚齿夹具及齿轮的安装1263
4.4 滚刀心轴和滚刀的安装要求1264
4.5 滚刀精度的选用1264
4.6 滚齿工艺参数的选择1264
4.7 滚齿调整1265
4.7.1 交换齿轮计算及滚齿机定数1265
4.7.2 滚刀安装角度、工作台回转方向及中间轮装置1265
4.8 滚切大质数齿轮1267
4.8.1 滚切大质数直齿圆柱齿轮时各组交换齿轮计算1267
4.8.2 滚切大质数斜齿圆柱齿轮时各组交换齿轮计算1267
4.8.3 Y38滚齿机加工大质数直齿圆柱齿轮时,分度、差动交换齿轮表1268
4.8.4 p的推荐值1268
4.9 滚齿加工常见缺陷及解决方法1268
5 交换齿轮表1271
6 插齿1275
6.1 插齿机的组成及传动系统1275
6.2 插齿机的基本参数和工作精度1277
6.2.1 插齿机的基本参数1277
6.2.2 常用插齿机的工作精度1277
6.3 常用插齿机连接尺寸1277
6.4 插齿刀的调整1278
6.5 插齿用夹具及调整1280
6.6 常用插齿机交换齿轮计算1281
6.7 插削余量及插削用量的选用1281
6.8 插齿加工中常出现的缺陷及解决方法1282
7 剃齿1284
7.1 剃齿机及其精度要求1284
7.2 剃齿刀的基本尺寸1285
7.3 剃齿用心轴1285
7.4 剃齿的切削用量1286
7.5 剃齿加工余量1287
7.6 剃齿方法1287
7.6.1 剃齿机与刀具、夹具的调整精度1287
7.6.2 轴交角的调整1288
7.6.3 常用的剃齿方法1288
7.7 剃齿误差与轮齿接触区偏差1289
7.7.1 剃齿误差产生原因及解决方法1289
7.7.2 轮齿接触区的偏差与修正方法1290
第6节 磨削加工1291
1 常见的磨削方式1291
2 磨削加工基础1292
2.1 砂轮安装与修整1292
2.2 砂轮修整工具及其选用1293
2.3 常用磨削液的名称及性能1294
3 外圆磨削1295
3.1 外圆磨削常用方法1295
3.2 工件的装夹1297
3.3 砂轮的选择1299
3.4 外圆磨削切削用量的选择1299
3.5 外圆磨削余量1301
3.6 外圆磨削常见的工件缺陷、产生原因及解决方法1302
4 内圆磨削1303
4.1 内圆磨削常用方法1303
4.2 工件的装夹1305
4.3 内圆磨削砂轮的选择及安装1306
4.4 内圆磨削切削用量的选择1308
4.5 内圆磨削余量的合理选择1312
4.6 内圆磨削常见的工件缺陷、产生原因及解决方法1313
5 圆锥面磨削1313
5.1 圆锥面的磨削方法1313
5.2 圆锥面的精度检验1315
5.3 圆锥面磨削的质量分析1316
6 平面磨削1317
6.1 平面磨削形式及特点1317
6.2 平面磨削常用方法1318
6.3 工件的装夹方法1321
6.4 平面磨削砂轮的选择1324
6.5 平面磨削切削用量的选择1324
6.6 平面磨削余量的合理选择1328
6.7 平面磨削的质量分析1328
7 成形磨削1329
7.1 成形磨削的几种方法1329
7.2 成形砂轮的修整1330
8 薄片工件磨削1333
9 细长轴磨削1334
10 刀具刃磨1334
10.1 工具磨床主要附件及其应用1334
10.2 刀具刃磨砂轮的选择1336
10.3 砂轮和支片安装位置的确定1338
10.4 刀具刃磨实例1338
11 高效与低粗糙度磨削1342
11.1 高速磨削1342
11.2 宽砂轮磨削1344
11.3 低粗糙度磨削1345
第7节 光整加工1347
1 研磨1347
1.1 研磨的分类及适用范围1347
1.2 研磨剂1347
1.2.1 常用磨料及适用范围1347
1.2.2 磨料粒度的选择1348
1.2.3 研磨液1348
1.2.4 研磨剂的配制1348
1.3 研具1349
1.3.1 研具材料1349
1.3.2 通用研具1350
1.4 研磨方法1352
1.4.1 常用研磨运动轨迹1352
1.4.2 研具的压砂1353
1.4.3 研磨工艺参数的选择1353
1.4.4 典型面研磨方法举例1354
1.5 研磨的质量分析1355
2 珩磨1356
2.1 珩磨机1356
2.2 珩磨头结构及连接方式1361
2.2.1 常用珩磨头结构形式1361
2.2.2 珩磨头的连接方式1363
2.3 珩磨用夹具1364
2.3.1 珩磨加工常用夹具结构形式1364
2.3.2 珩磨加工中的对中1364
2.4 珩磨油石的选择1366
2.4.1 珩磨油石磨料的选择1366
2.4.2 珩磨油石磨料粒度的选择1366
2.4.3 珩磨油石硬度的选择1367
2.4.4 结合剂的选择1367
2.4.5 组织和浓度的选择1367
2.4.6 珩磨油石长度的选择1367
2.4.7 珩磨油石数量和宽度的选择1367
2.5 珩磨工艺参数的选择1367
2.5.1 珩磨速度和珩磨交叉角1367
2.5.2 珩磨油石的工作压力1368
2.5.3 珩磨油石的行程1368
2.5.4 珩磨余量的选择1369
2.5.5 珩磨液的选择1369
2.5.6 对工件珩磨前的要求1369
2.6 珩磨的质量分析1369
3 抛光1372
3.1 抛光轮材料的选用1372
3.2 磨料和抛光剂1373
3.3 抛光工艺参数1373
第8节 钻削、扩削、铰削加工1374
1 钻削1374
1.1 典型钻头举例1374
1.1.1 群钻1374
1.1.2 几种典型钻头举例1379
1.2 钻削方法1380
1.2.1 常用装夹方法1380
1.2.2 常用钻夹具(钻模)形式及特点1381
1.2.3 钻削不同孔距精度所用的加工方法1381
1.2.4 切削液的选用1382
1.2.5 常用钻孔方法1382
1.2.6 特殊孔的钻削方法1382
1.3 钻削加工切削用量的选择1384
1.3.1 高速钢钻头钻削不同材料的切削用量1384
1.3.2 硬质合金钻头钻削不同材料的切削用量1385
1.3.3 群钻加工钢件时的切削用量1387
1.3.4 群钻加工铸铁件时的切削用量1387
1.4 麻花钻钻孔中常见问题产生原因和解决方法1388
2 扩孔1390
2.1 扩孔方法1390
2.2 扩孔钻的切削用量1390
2.3 扩孔钻扩孔中常见问题产生原因和解决方法1391
3 锪孔1392
3.1 锪钻1392
3.2 高速钢及硬质合金锪钻加工的切削用量1393
3.3 锪孔中常见问题产生原因和解决方法1393
4 深孔钻削1393
4.1 深孔钻削的适用范围、加工精度与表面粗糙度1393
4.2 深孔加工中每次进给深度1394
4.3 内排屑深孔钻钻孔中常见问题产生原因和解决方法1394
5 铰削1395
5.1 铰削方法1395
5.1.1 铰刀直径的确定及铰刀的研磨1395
5.1.2 铰刀在使用中的修磨1396
5.1.3 铰削余量的选择1396
5.1.4 铰削时切削液的选用1397
5.1.5 手工铰孔应注意的事项1397
5.1.6 机动铰孔应注意的事项1397
5.1.7 圆锥孔的铰削1397
5.2 铰削加工切削用量的选择1398
5.2.1 铰刀磨钝标准及寿命1398
5.2.2 铰削用量1398
5.3 多刃铰刀铰孔中常见问题产生原因和解决方法1400
第9节 镗削加工1402
1 镗刀1402
1.1 单刃镗刀1402
1.2 双刃镗刀1402
1.3 复合镗刀1404
1.4 微调镗刀1406
1.5 镗床用攻螺纹夹头1407
2 卧式镗床镗削1407
2.1 卧式镗床基本工作范围1408
2.2 卧式镗床基本定位方法1409
2.2.1 主轴轴线与镗孔轴线重合方法1409
2.2.2 主轴轴线与后立柱刀杆支架轴线重合方法1409
2.3 导向装置布置的形式与特点1409
2.4 工件定位基准及定位方法1409
2.5 镗削基本类型及加工精度分析1414
2.5.1 悬伸镗削基本方式及加工精度分析1414
2.5.2 支承镗削基本方式及加工精度分析1414
2.6 镗削加工1417
2.6.1 镗刀安装与对刀1417
2.6.2 粗镗、精镗1417
2.6.3 基本镗削方法1418
2.6.4 用镗模加工方法1426
2.6.5 镗孔坐标尺寸的计算1426
2.6.6 卧式镗床的镗削用量1428
2.6.7 卧式镗床常用测量方法及精度1429
2.6.8 卧式镗床加工中常见的质量问题与解决方法1430
3 坐标镗床镗削1431
3.1 坐标换算和加工调整1431
3.2 找正工具与找正方法1431
3.3 坐标测量1431
3.4 坐标镗床的镗削用量1436
3.5 镗削加工质量分析1436
4 精镗床加工1437
4.1 精镗床的加工精度1437
4.2 精镗床镗刀几何参数的选择1437
4.3 精镗床加工操作要求1439
4.4 精镗床的精密镗削用量1439
第10节 刨削、插削加工1440
1 刨削1440
1.1 刨削加工方法1440
1.1.1 牛头刨床常见加工方法1440
1.1.2 龙门刨床常见加工方法1440
1.2 刨刀类型及切削角度的选择1440
1.2.1 刨刀的结构形式1440
1.2.2 常用刨刀的种类及用途1440
1.2.3 刨刀切削角度的选择1440
1.3 刨削常用装夹方法1440
1.4 刨削工具1440
1.5 槽类工件的刨削与切断1440
1.6 镶条的刨削1440
1.7 刨削的经济加工精度1449
1.8 常用刨削用量1449
1.9 刨削常见问题产生原因及解决方法1449
1.9.1 刨平面常见问题产生原因及解决方法1449
1.9.2 刨垂直面和阶台常见问题产生原因及解决方法1449
1.9.3 切断、刨直槽及T形槽常见问题产生原因及解决方法1449
1.9.4 刨斜面、V形槽及镶条常见问题产生原因及解决方法1449
1.10 精刨1449
1.10.1 精刨的类型及特点1454
1.10.2 精刨加工对工艺系统的要求1455
1.10.3 精刨表面常见问题产生原因及解决方法1456
2 插削1458
2.1 常用插削方式和加工方法1458
2.2 插刀1458
2.3 插平面及插槽的进给量1458
2.4 插削键槽常见缺陷产生原因及解决方法1458
第11节 拉削加工1463
1 常见拉削加工分类的特点及应用1463
2 拉削方式1467
3 拉削装置1468
4 拉刀1469
4.1 拉刀的类型1469
4.2 拉刀的基本结构及刀齿的几何参数1469
5 拉削经济加工精度及表面粗糙度1471
6 拉削工艺参数1471
6.1 拉削前对工件的要求1471
6.2 拉削余量的选择1471
6.3 拉削用量1471
6.4 拉削用切削液1471
7 拉削中常见缺陷产生原因与解决方法1474
第12节 难加工材料的切削加工1476
1 常用的难切削材料及应用1476
2 难切削金属材料的可加工性比较1477
3 高锰钢的切削加工1477
3.1 常用切削高锰钢的刀具材料1477
3.2 切削高锰钢车刀与铣刀的主要角度1477
3.3 常用硬质合金刀具车削、铣削高锰钢的切削用量1478
4 高强度钢的切削加工1478
4.1 常用的切削高强度钢用高速钢刀具材料1478
4.2 常用的切削高强度钢用硬质合金1478
4.3 切削高强度钢的车刀与铣刀的主要角度1478
4.4 车削高强度钢的切削用量1478
4.5 按工件硬度选择铣削用量1479
5 高温合金的切削加工1479
5.1 常用切削高温合金的刀具材料1479
5.2 车削高温合金常用刀具的前角与后角1479
5.3 车削高温合金切削用量举例1480
5.4 铣削高温合金切削用量举例1481
6 钛合金的切削加工1482
6.1 常用切削钛合金的刀具材料1482
6.2 切削钛合金的车刀与铣刀的主要角度1482
6.3 车削钛合金切削用量1483
6.4 铣削钛合金切削用量1483
7 不锈钢的切削加工1484
7.1 常用切削不锈钢的刀具材料1484
7.2 切削不锈钢的车刀与铣刀的主要角度1484
7.3 车削不锈钢的切削用量1485
7.4 高速钢铣刀铣削不锈钢的切削用量1485
第12章 钳工加工及装配1486
第1节 钳工加工1486
1 划线1486
1.1 常用划线工具名称及用途1486
1.2 划线常用的基本方法1490
1.3 划线基准的选择1493
1.3.1 划线基准选择原则1493
1.3.2 常用划线基准类型1493
1.4 划线时的校正和借料1493
1.5 划线程序1496
1.6 立体划线1496
1.7 应用分度头划线1498
1.8 几种典型钣金展开图举例1499
1.8.1 一端斜截45°圆管1499
1.8.2 圆管弯头1499
1.8.3 直交等径三通管1500
1.8.4 斜接等径三通管1500
1.8.5 直交不等径三通管1501
1.8.6 等角V形等径三通管1501
2 锯削1502
2.1 锯削工具1502
2.1.1 锯架1502
2.1.2 锯条1503
2.2 锯削方法1504
3 錾削1506
3.1 錾子的种类及用途1506
3.2 錾子切削部分及几何角度1507
3.3 錾子的刃磨及淬火方法1507
3.4 錾削方法1508
4 锉削1510
4.1 锉刀的各部名称1510
4.2 锉刀的分类及基本参数1510
4.3 常用锉刀形式及尺寸1512
4.3.1 钳工锉1512
4.3.2 整形锉1515
4.3.3 异形锉1520
4.4 锉刀的选用1522
4.5 锉削方法1523